Rivian’s Path to Better Quality Control
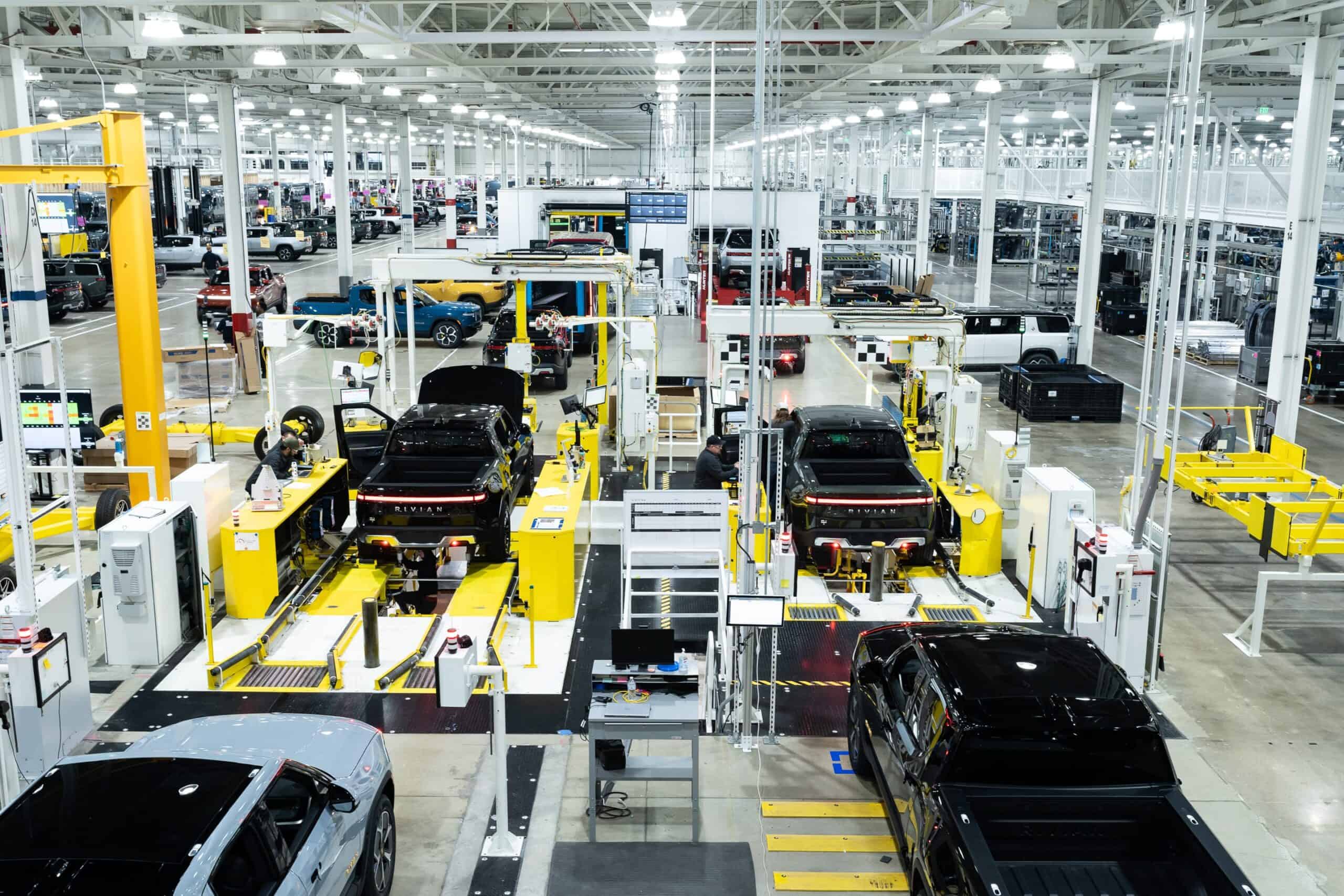
In electric vehicles, the road from concept to showroom is anything but smooth. Rivian, one of the most anticipated new EV manufacturers, has faced scrutiny that only comes with high expectations. As customers express excitement and pride over owning one of Rivian’s groundbreaking R1T trucks or R1S SUVs, there has also been a wave of feedback and criticism over the initial quality control issues in these early models. What many forget, however, is that even Tesla – the world’s most famous EV brand – faced similar growing pains, and to some extent still does.
This article dives into Rivian’s quality journey, looking at the parallels with Tesla’s early days, improvements in Rivian’s second-generation models, and the iterative challenges that all new automakers face.
Rivian’s Initial Quality Issues: Learning from Tesla’s Path
When Tesla launched the Model 3 and Model Y, the vehicles promised revolutionary design, high-tech features, and zero-emission appeal at an accessible price point. However, many early customers were met with issues in build quality. Common complaints involved panel gaps, inconsistent paint jobs, door alignment problems, and software glitches. The media spotlight didn’t do Tesla any favors; every hiccup in quality control was magnified as consumers weighed the cost of their investment against these early missteps.
Rivian is navigating similar territory, as early owners and enthusiasts report issues with panel gaps, uneven paint application, and other minor build inconsistencies. For Rivian, much like it was for Tesla, these quality concerns stem from being a new manufacturer ramping up production. Moving from prototypes to full-scale production is a massive challenge, especially when the expectations for a premium build are set sky-high.
While Tesla’s early struggles didn’t stop it from becoming a dominant force in the EV industry, Rivian has shown it’s committed to the same path of improvement. Customer feedback has driven Rivian to introduce changes quickly, culminating in its second-generation models of the R1T and R1S.
The Impact of Iterative Improvements: Rivian’s Gen 2 Vehicles
For Rivian, the Gen 2 R1T and R1S models are a testament to learning from feedback and investing in quality control. The new generation shows improvements in various areas that customers pointed out in Gen 1 models. For instance, Rivian has addressed panel alignment, enhanced paint consistency, and made improvements to interior material durability. These changes reflect a dedication to quality that goes beyond surface-level fixes. It should be stated that of course there will still be issues and nothing is ever 100%.
Yet, even as Gen 2 shows these advancements, new challenges are surfacing. Certain components introduced to improve functionality or comfort have presented fresh quality concerns. These “two steps forward, one step back” moments are characteristic of fast-moving, young companies that are navigating the dual demands of scaling up production and refining build quality simultaneously. Rivian has already shown a commitment to addressing these issues, proving that each iteration brings new opportunities for growth and refinement.
Navigating the Quality Control Journey as a New EV Maker
Unlike established automakers, Rivian and Tesla must balance innovation with quality. They aren’t just producing cars; they’re also bringing groundbreaking technology to the market. This balancing act between innovation and quality can result in temporary lapses in quality control, which in turn lead to criticism and often disappointment for early adopters.
However, Rivian, like Tesla, has a significant advantage over legacy automakers: the ability to quickly deploy over-the-air (OTA) updates. These updates allow Rivian to fix software issues, improve vehicle performance, and enhance user experience without requiring customers to visit service centers. Tesla paved the way here, showing how an OTA update can be an effective tool in addressing early quality issues, both in functionality and in customer trust.
Another valuable tool has been direct customer feedback. Rivian has actively engaged with its community, acknowledging issues and working toward solutions – a strategy that not only fosters goodwill but also offers valuable real-time insights for improvement.
The Future of Rivian and Quality Control in the EV Industry
As Rivian scales its production, quality expectations will continue to rise. If Tesla’s path is any indication, Rivian will likely see steady improvement as it expands. By addressing quality concerns promptly and engaging directly with customers, Rivian is building a reputation for responsiveness and dedication to improvement.
The growing pains of new automakers don’t typically define their long-term trajectory – it’s how they handle these challenges that make the difference. Tesla’s early quality control issues didn’t prevent it from becoming an EV powerhouse, and there’s little doubt that Rivian is on a similar track. With time, Rivian will likely find its stride and reach a level of consistency in build quality that will meet the high standards of its enthusiastic customers.
The Road Forward
Rivian’s journey is a reminder that automotive quality control is a process, not a destination. While initial quality issues have sparked criticism, these are standard growing pains for any new automaker, particularly in the fast-evolving EV sector. Rivian has shown a commitment to listening, iterating, and improving, much like Tesla did – and still does. For EV enthusiasts and Rivian customers alike, these improvements are a promising sign of a maturing company poised to make a lasting impact on the EV landscape.